3 Intended resetting
3.1 Importance of human intention in resetting
Since an emergency stop switch is primarily used by an intended action during an emergency situation, the importance of an intended action in its resetting the emergency stop switch is also described in the safety requirements.
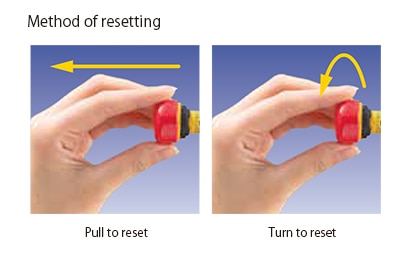
ISO13850:2015(JIS B9703:2019) 4.1.1.2 The emergency stop function shall be reset by intentional human action. Resetting of the emergency stop function shall be operated by disengagement of an emergency stop device. |
3.2 Description concerning reset in the instruction manual
Since an emergency stop switch is primarily used in an emergency situation, information concerning machine reset is described in the safety requirements.
ISO13850:2015(JIS B9703:2019) 4.1.4 Disengagement (e.g. unlatching) of the emergency stop device The instructions for use of the machine shall state that, after actuation and before disengaging the device(s), the machinery shall be inspected in order to detect the reason for actuation. |
The actuation of an emergency stop switch means that there is a possibility that an emergency situation has occurred. Therefore, before resetting the emergency stop switch, it is necessary to check the cause of the actuation and confirm that safety is ensured. Since it is necessary to disseminate this information to users, the instruction manual must describe the inspections required after actuating and before resetting emergency stop switches.
3.3 Unrecommended reset type
The use of some emergency stop devices is no longer recommended after the revision. Although their use is not prohibited, the following conditions must be satisfied to use those devices.
ISO13850:2015(JIS B9703:2019) 4.3.6 Emergency stop device requiring a key on the actuator to be disengaged (unlatched) should be avoided. When an emergency stop actuator can only be disengaged by using a key, to avoid injuries to hands; — Instruction for use of the machine shall describe the correct use of the key. — Provide a warning that the key should only be in the actuator of the device to disengage the actuator. |
These safety requirements were added because of the following. A key to reset the emergency stop switch may be left inserted into an actuator. If a person unaware of the situation operates the emergency stop switch without thinking carefully in an emergency, the person can injure his/her hand with the key inserted into the actuator. Therefore, the use of the key reset type emergency stop switch is no longer recommended.
In addition, when using a key reset type emergency stop switch after performing the risk assessment, implement measures based on the above safety requirements.
4 Prevention of unintended reset
As described above, human intention plays an important role in the emergency stop function. Intended actuations, prevention of unintended actuations, and intended reset operations are specified in the standards. Note that prevention of unintended reset operations is not specified as a safety requirement.
However, “Prevention of unintended reset operation” and the “Intended reset operation” are both important as a practical matter. The prevention of an unintended reset operation requires special attention if multiple persons enter a danger zone, for example, during machine setup or maintenance. In order to prevent an unintended reset, the key reset type emergency stop switches, shown in Section 3.3, have conventionally been used. As mentioned above, this is no longer recommended. Therefore, another measure to prevent an unintended reset is necessary.
The use of a padlock to protect the emergency stop switch is one such alternative measure. As shown in the figure below, only after actuating the emergency stop switch, each worker can padlock the switch with his/her own padlock. By keeping the key to himself/herself, an unauthorized reset by other workers can be prevented. Since the machine will not be restarted, each worker can ensure his/her own safety.
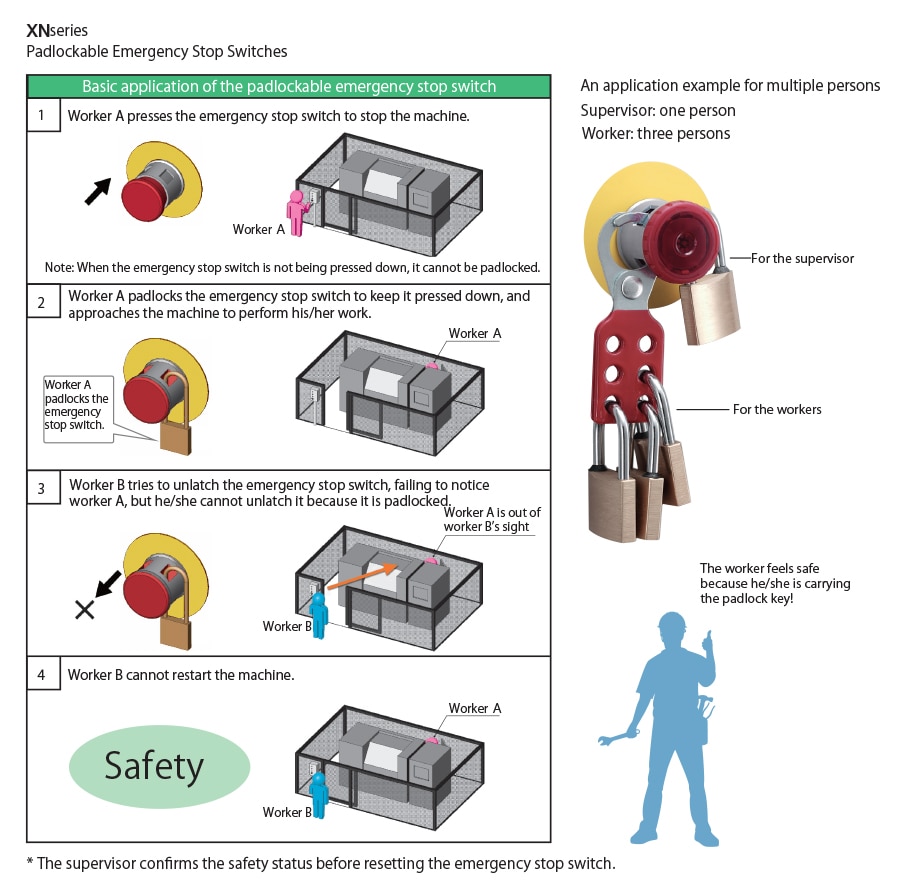
According to your applications, use the following padlockable emergency stop switches.